PVC (polyvinyl chloride) is one of the five most widely used thermoplastics in the world, which has wide applications in various industries due to its unique properties. However, PVC alone cannot be processed in its pure form, and to improve its properties and increase efficiency, it is usually necessary to add several additives.
1- Essential additives in PVC foam production
In the production of PVC foamed sheet, several types of additives are used, including the following:
- Thermal stabilizers: These materials help prevent the decomposition of PVC at high temperatures and increase the useful life of the product.
- Internal and external lubricants: These additives help improve the flow of materials during the production process and prevent materials from sticking to equipment.
- Process aids: These materials help improve the production process and reduce energy consumption.
- Impact modifiers: These additives help increase the physical resistance of the sheets to impact and breakage.
In addition, in the production of PVC foamed sheets, foaming agents and melt viscosity controllers are also used as key additives. These materials help control the foam structure and ultimately improve the quality of the final product.
2- Initial production stages
The production process of PVC foamed sheets usually begins with physical mixing in a mixer. In modern methods, high-speed turbo mixers are used that heat the PVC powder by creating frictional heat. At this stage, additives are added to the PVC powder and the heat causes these materials to penetrate the surfaces of the PVC particles. This penetration helps improve the physical and chemical properties of the final product.
After this stage, the heated powder is cooled and stored. This process helps maintain the quality of the raw materials and prevent their decomposition.
3- Extrusion process
The mixed materials then enter the production line, which is usually made up of twin-screw extruders. Due to their special design, these extruders allow for uniform mixing and melting of the materials. At this stage, the materials are melted due to friction and heat. Extrusion is the main process for producing PVC foams.
In this stage, the resins and additives are combined, and at the end of the extruder, the heat generated activates the foaming agent. This foaming agent usually contains chemicals that release carbon dioxide or nitrogen gas when heated.
4- Foaming action
The released gas creates tiny pores in the PVC. These pores make the foamed sheet lighter and better insulated against heat and sound. By controlling the conditions and using process aids, the size of the pores can be adjusted. Foam formation is a key step in the extrusion process.
5- Cell growth and foam structure
Cell growth continues until the pressure inside the bubbles equals the surface tension of the bubble walls. If this balance is not maintained, the cell structure may collapse. For this reason, it is very important to control the temperature, pressure, and viscosity of the melt before it leaves the system.
Various factors such as the type and amount of gas produced, the temperature and pressure of the system, and the cooling rate have a great impact on the structure and morphology of the foam. For example, increasing the temperature can increase the size of the pores, while decreasing the temperature can lead to denser foams.
6- Calibration and final cutting
After production, the foamed sheets are passed through the die. At this stage, the calibrator system fixes the dimensions of the sheets. This calibration requires high accuracy to maintain the final quality of the product.
Finally, the edges of the sheet are cut and divided into the desired length and width. These sheets are then prepared for packaging. PVC foamed sheets are widely used in the cabinet-making industry, interior decoration, packaging, and even in the manufacturing of electrical and electronic products.
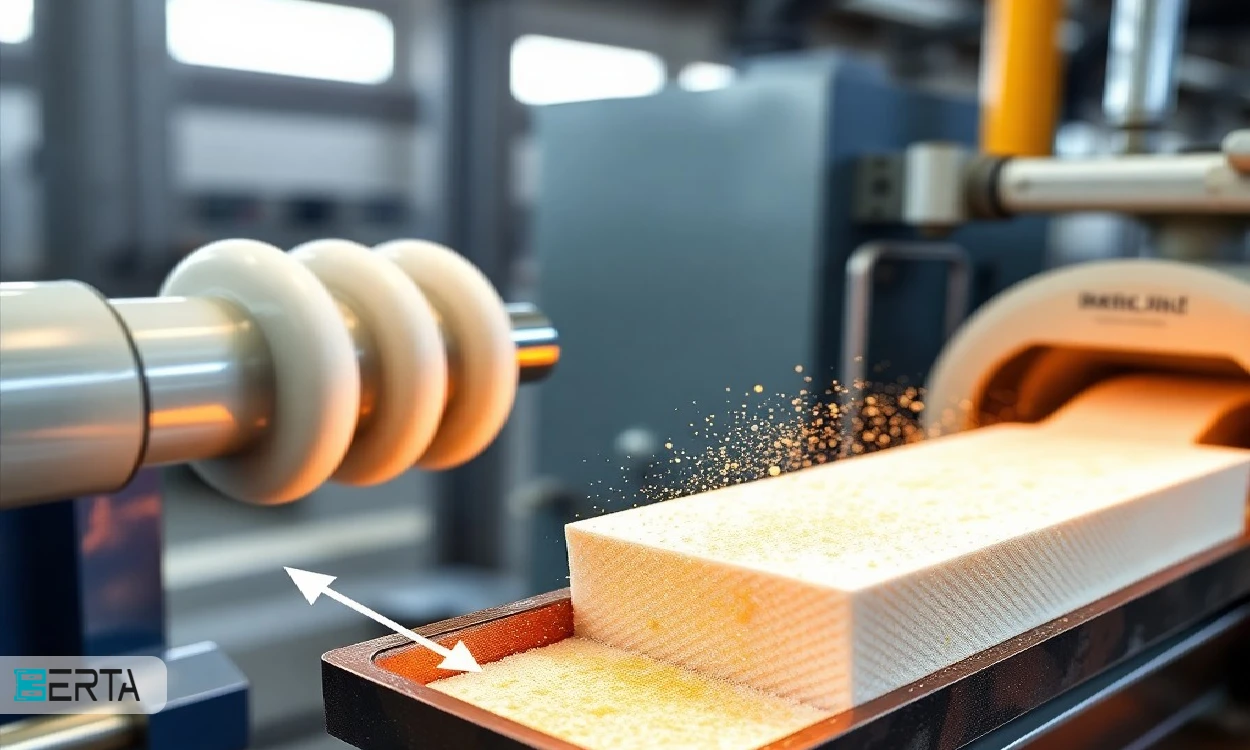
Conclusion
By carefully observing the production steps and controlling the conditions, it is possible to produce high-quality PVC foamed sheets with desirable properties that have wide applications in various industries. This process not only helps to improve the quality of the products but also leads to a reduction in production costs. Finally, PVC foamed sheets are a good choice for many applications in various industries due to their unique characteristics.